Car park construction involves the planning, design, and building of parking facilities to accommodate vehicles safely and efficiently. The process of car park construction includes; site preparation, laying foundations, constructing the parking surface and installing features such as lighting, signage, drainage, and barriers. Effective car park construction provides durability, safety, and optimal use of space. This premise remains true regardless of whether it is the construction of a huge multi-storey car park or a small local one. Good car park construction needs to meet the need of both car park users and facility operators.
Car Park Waterproofing Systems support car park construction projects by delivering specialist services in surfacing, waterproofing, and line marking. While we do not undertake full structural construction, we work closely with main contractors and developers to complete the final stages of the build. Our team installs high-performance surfacing systems, applies advanced waterproofing membranes, and provides durable, high-visibility markings to ensure the finished car park is safe, functional, and built to last. Whether for new builds or major refurbishments, Car Park Waterproofing Systems ensure every finished surface meets the highest standards of performance, waterproofing and presentation.
What Is Car Park Construction?
Car park construction involves three main stages; planning, car park design, and the building of parking facilities. The objective of car park construction is to accommodate vehicles safely and efficiently. The process of car park construction begins with site preparation. Site preparation involves clearing the area, leveling the ground, and ensuring proper drainage systems are in place. The construction phase normally includes laying foundations, erecting structural elements, and surfacing the parking area. The surfacing is done with durable materials such as asphalt, mastic asphalt and concrete.
Car park construction also includes the installation of features such as lighting, signage, barriers, and entry/exit control systems. All of these features enhance the safety and functionality of the parking space. Modern car park construction is more frequently integrating sustainable practices, this includes permeable paving and green spaces. Throughout the car park construction process compliance with local building codes and safety regulations is crucial to guarantee a facility which is both safe and legally compliant. Overall, car park construction aims to create a durable, functional, and user-friendly car park which that meets the needs of users and facility operators.
Have a question about an upcoming project?
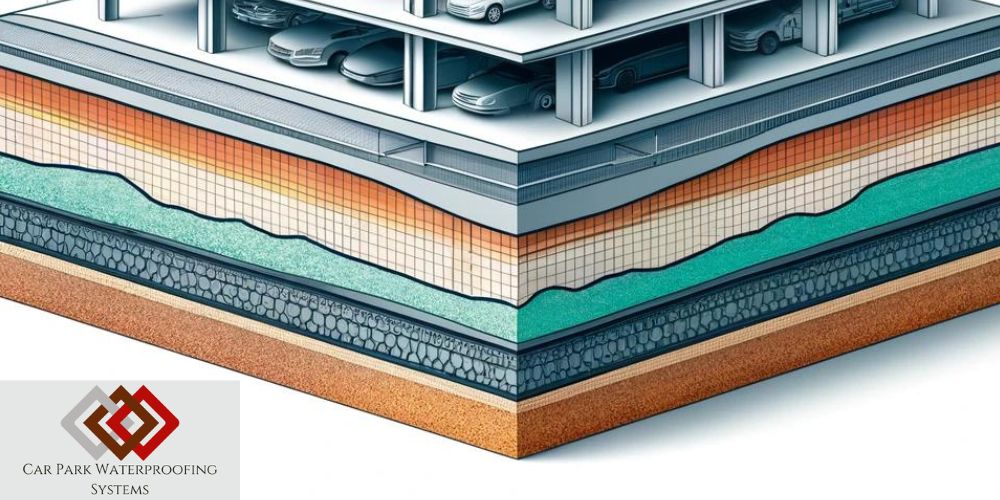
What Is The Process Of Car Park Construction?
The process of car park construction involves multiple steps to ensure a durable and functional parking facility. From initial planning and car park design to the final inspection and opening, each phase is important to deliver a high quality parking facility. Below we will look at each of these stages in more detail.
- Planning and Design
- Site Preparation
- Foundation Construction
- Drainage Installation
- Sub-Base and Base Layer Installation
- Surfacing
- Marking and Signage
- Lighting and Security Installation
- Landscaping
- Final Inspection and Testing
- Opening and Maintenance Planning
1. Planning and Design
The initial step in car park construction is planning and design. When planning and designing a car park in the UK, it's important to start with a feasibility study to determine the need and viability of the project. This involves understanding current and future demands for parking. The potential environmental impact of new car park construction must also be understood. The design phase comes next. Car park design focuses on creating a plan which details layout, capacity, access points and essential infrastructure. Essential infrastructure includes drainage, lighting, and safety features. A new car park typically aims for a capacity of 100 to 300 parking spaces per acre in urban locations.
During the planning and design process it is crucial to refer to guidelines set out by the UK's Institution of Structural Engineers who provide standards for safety and design. Also at this stage the necessary permits and approvals from local authorities must be secured. THis can include compliance with the UK Building Regulations Part M, covering accessibility, and Part F, regarding ventilation. All of these steps are vital to make sure the car park meets both current needs and regulatory standards. Success at the planning and design stages ensures the project is set up for successful implementation.
2. Site Preparation
Site preparation is an essential part of car park construction. The purpose of site preparation is to focus on preparing the area for the structural development of the car park. The site preparation phase involves the complete removal of all existing structures, vegetation, and debris on the site. Next, detailed site grading is carried out. Site grading is done to ensure a level base. A level base is crucial for the proper installation of subsequent layers and for effective drainage systems. The prevention of water accumulation is one of the most vital parts of car park construction as this prevents potential structural damage. Proper drainage is pivotal in doing this. This is especially true in the UK where there is frequent rainfall. This large amount of rainfall has the potential to impact the integrity of car park surfacing if not managed correctly.
Comprehensive soil testing is also conducted at the site preparation stage. Soil testing is done to evaluate the suitability of the ground for supporting the planned structures. These soil tests indicate soil composition, bearing capacity, and any potential for subsidence. All of these are critical for designing a foundation which adheres to safety and durability standards. UK Building Regulations states soil assessments must address specific geotechnical and environmental considerations. This is done to ensure the car park has a foundation which is stable and sustainable. The site preparation stage is important for ensuring durable, safe, and compliant car park structures.
3. Foundation Construction
Foundation construction is critical in providing long-term durability and functionality for car park structures. The first step of foundation construction is the base layer. This base layer is made up of compacted gravel or crushed stone. The purpose of this base layer is to evenly distribute weight and provide structural integrity for the car park. UK construction standards state the base layer is normally 150 to 300mm (5.906 to 11.811 inches) thick. The thickness is decided based upon the expected load and traffic conditions the car park must endure. The objective with this base layer is to make sure the car park can withstand the pressures of daily use.
The base layer may also need to integrate geotextile fabrics which are used to improve soil stability and drainage. These geotextile fabrics are often used in areas with poor soil conditions. These fabrics are used to separate different soil layers and facilitate water flow away from the foundation. Diverting water away from the foundation is vital in order to prevent issues such as waterlogging. Research by Ground Engineering Journal states the use of geotextile can extend the lifespan of a car park's foundation significantly. The reason for this it reduces maintenance needs by preventing common issues like rutting and potholes. This makes using geotextile fabrics a wise investment for long-term infrastructure sustainability.
4. Drainage Installation
The drainage installation phase of car park construction is crucial to manage stormwater and prevent water accumulation. An effective drainage system is a critical feature of any car park which is to have a long lifespan. A drainage system helps prevent surface water pooling. Pooling water can can lead to a car park suffering from structural damage and dangerous conditions. The drainage system installation process involves the installation of pipes, drains, and catch basins. All of these are specified in the car park design plan and their purpose is to ensure efficient water removal. According to CIRIA, a well-designed drainage system reduce maintenance costs and extend the lifespan of car park surfaces by preventing water-related issues such as potholes and cracks. In the UK, adhering to drainage regulations and standards is essential to ensure environmental compliance and sustainability. Studies by the British Parking Association found proper drainage systems can reduce surface repair costs by up to 30%. This highlights the importance of drainage in car park construction. One the drainage system is installed the sub-base and base layer can be installed.
5. Sub-Base and Base Layer Installation
The next stage of car park construction is sub-base and base layer installation. The sub-base normally consists of crushed stone or gravel. The sub-base is laid and compacted. This sub-base layer is essential for providing a stable foundation for the car park. The sub-base distributes loads and improves the drainage. According to the Department for Transport, a well-constructed sub-base can greatly enhance the durability and performance of the car park surface. Normally, the sub-base layer will be a minimum of 150mm thick. However, this thickness can vary depending on ground conditions and the traffic loads the car park will be subjected to.
Next, the base layer is added to provide extra strength and stability. This base layer is different to the base layer in the foundation construction stage. The base layer at this state is again made up of crushed stone or gravel but is finer and more precisely graded. This base layer is compacted with attention being paid to meet the necessary thickness and compaction standards. The thickness of the base layer is normally around 100mm to 150mm (3.937 to 5.906 inches). This thickness depends on the specific design requirements. Research by TRL (Transport Research Laboratory) shows proper compaction of the base layer can extend the life of a pavement by reducing the risk of deformation and ensuring a smooth, even surface. In the UK, adhering to thickness and compaction standards is crucial for creating a durable and long-lasting car park structure. Once sub-base and base layer is installed, the car park is ready for surfacing.
6. Surfacing
Surfacing is the next step in the car park construction process. The chosen surface material (normally asphalt or concrete) is applied across the base layer of the concrete. It is important to make sure there is an even distribution and thickness of the chosen surfacing material. The UK Department for Transport state the typical thickness for asphalt surfacing on car parks ranges from 40mm to 50mm, while concrete surfaces may require a thickness of 100mm or more. The thickness of the surfacing layer will be dependent on the expected load bearing requirements of the car park. Compact the surface material using rollers to achieve a smooth and durable finish. Proper compaction of the surfacing layer is vital. Compaction prevents surface irregularities and ensures the long-term durability of the surfacing layer. Research by the Transport Research Laboratory indicates well-compacted asphalt can extend the lifespan of a car park surface by up to 25%. The obvious benefit of extending the service life of a car park surface is reduced maintenance costs.
Once surfacing is complete it is common for waterproofing to be applied. This is normally a car park coating such as mastic asphalt or a liquid applied membrane. Coatings such as asphalt, polyurethane or polyurea, provide an extra layer of protection. This extra waterproof barrier further shields the car park surface against water ingress and increases the life expectancy of the car park surface. Research from the Building Research Establishment found, liquid waterproofing systems can reduce water damage and extend the lifespan of car park surfaces by preventing the cracks and potholes triggered by freeze-thaw cycles. This is very relevant in the UK, as car parks must endure frequent rainfall and a range of weather conditions. Exposed decks such as those on the top floor of multi-storey car parks would benefit the most from a car park surface waterproofing layer.
7. Marking and Signage
Once the car park surfacing and any waterproofing layer is complete, the next part of the car park construction process is marking and signage. Good car park design sets out the optimal way for traffic to be managed in the parking facility. Marking and signage plays a huge role in making a car park layout user friendly. At this stage of the car park construction process line marking are applied to the car park surface to create parking bays, arrows to control traffic flow and to signify pedestrian areas. This step is essential for maximising the efficiency and safety of the car park. The British Parking Association state car parks with clear and visible markings can decrease the possibility of accidents and improve car park user satisfaction. Car parks in the UK often use of thermoplastic road markings to maximise the long term effectiveness of markings. The expected lifespan of thermoplastic road markings is 5 to 8 years under normal conditions.
Signage is also installed at this stage of the car park constriction process. Signage is used to show directions, parking levels, parking restrictions, and safety information. Good signage helps optimise the flow of vehicles and ensuring compliance with parking regulations. Traffic flow is particularly important in car parks which can get close to capacity, for example Shopping Centres in the Christmas period. The Department for Transport recommends using reflective materials for signs to maximise visibility. Good visibility of signs is crucial in low-light conditions. Research by the Transport Research Laboratory indicates well-placed and clearly visible signage can reduce incidents of improper parking and enhance the overall safety of car parks. This need for good visibility is increased for in larger car parks where navigation can be more complex. Once markings and signage are installed into the car park the next step is lighting and security installation.
8. Lighting and Security Installation
Lighting and security installation are the next part of the car park construction process. Lighting is vital to provide adequate illumination for both safety and security purposes. Good lighting reduces the risk of accidents and deters criminal activity. Research from the British Parking Association states well-lit car parks can reduce crime by up to 30%. In the UK, it is imperative to meet the standards set by the Institution of Lighting Professionals (ILP) for public parking facilities. To maximise energy efficiency of the car parks can make use of LED lighting and lighting charged by solar panels. Security installations include; CCTV cameras and access control systems. According to the Home Office, the presence of CCTV in car parks can reduce vehicle-related crime by up to 51%. Both CCTV cameras and access control systems can greatly improve the security of any parking facility.
9. Landscaping
Landscaping is used towards the end of the car park construction process to provide shade and aesthetic appeal. This is achieved by planting trees, shrubs, and grass. The Royal Horticultural Society (RHS) state adding greenery to urban spaces can vastly improve air quality and create a more pleasant environment. When used for car parks it is important landscaping does not obstruct visibility or access. Well designed landscaping should complement the car park's functionality, whilst providing environmental and aesthetic benefits. Once a parking facility has been landscaped the next step is a final inspection and testing.
10. Final Inspection and Testing
The penultimate stage of car park construction is the final inspection and testing. A thorough inspection is conducted to make sure all aspects of the car park meet the required standards and specifications. This final inspection is critical imperative for checking the quality and compliance of the car park construction. The UK Health and Safety Executive (HSE) state final inspections may identify potential issues which need fixing prior to the car park opening to the public. Final inspections are very important as they ensure the safety and functionality of all new car parks. At this stage any necessary tests are performed. Testing includes; drainage performance and structural integrity checks. The Chartered Institution of Highways and Transportation (CIHT) say a thorough testing process can prevent future maintenance problems and increase the longevity of the car park structure. Once the final inspection and testing are successfully completed the final phase of car park construction is opening and maintenance planning.
11. Opening and Maintenance Planning
For car park opening and maintenance planning, the first stage is to prepare the car park for open day. When the construction process is finished the whole site should be cleaned and all car park features should be checked one last time. During this process lighting, signage, and drainage are all checked to confirm they are operating correctly. At this time a maintenance plan should also be developed to ensure the long-term functionality and safety of the car park. The Institution of Civil Engineers (ICE) recommends regular maintenance as a vital part of extending the lifespan of infrastructure and preventing costly repairs. By investing in a consistent maintenance plan, car park owners can keep their maintenance costs low, maximise potential revenue generation and get the best possible return on their investment.
What Are The Different Types Of Car Park Which Can Be Constructed?
There are a number of ways car parks can be constructed, this is normally dictated by the intended use of the car park, the budget and the spatial constraints. The different types of car park constructed which can be constructed are:
- Surface Car Parks
- Multi-Storey Car Parks
- Underground Car Parks
- Automated Car Parks
- Rooftop Car Parks
- Park and Ride Facilities
- Temporary Car Parks
- Valet Parking Facilities
If you require more information about car park construction or would like a quote for your project, click the button below. Our professional team is ready to assist you with all your construction needs.