Car Park Waterproofing Systems: Waterproofing, Coatings and Repairs Specialists
Car Park Waterproofing Systems are a leading provider of car park waterproofing solutions in the United Kingdom. Car Park Waterproofing Systems provide a full range of car park waterproofing services, including the waterproofing of decks, roofs, flooring, walkways, and steps. In addition to services relating to the waterproofing of car parks, Car Park Waterproofing Systems also provide the following services: car park repairs, car park refurbishment, car park coatings, car park expansion joints, and car park coatings. Car Park Waterproofing Systems are industry leaders in both the application of mastic asphalt and the use of innovative cold-applied liquid coatings. The combination of a skilled waterproofing team and access to the most innovative car park waterproofing products allows Car Park Waterproofing Systems to find the perfect solution for each car park they work on, while ensuring market-leading value for money. Car Park Waterproofing Systems are headquartered in Dunmow, Essex and provide car park waterproofing services across the United Kingdom.
Car park waterproofing refers to the process of applying protective coatings and membranes to car parks, in order to prevent water ingress. Water ingress is the unwanted penetration of water into a building or structure. Water ingress can cause damage which compromises the integrity of the building or structure. In the case of car parks, water ingress can cause damage such as corrosion, concrete deterioration, and steel reinforcement rust. Water ingress is prevented by applying waterproofing systems to the flooring of car parks. Car park waterproofing systems are designed to create a protective barrier against moisture, chemical attacks, and mechanical stress. Car park waterproofing is designed to ensure the longevity, structural integrity and safety of car parks. Car park waterproofing solutions must be able to vehicle usage and the environmental conditions which the car park must endure.
Below we will look at the various aspects of car park waterproofing. We will start with a basic definition of car park waterproofing, then look at the benefits of car park waterproofing. Then we will analyse the different car park waterproofing systems, including liquid-applied membranes, mastic asphalt and cementitious waterproofing. After we will provide a step-by-step guide of how to waterproof a car park. Then we will examine the costs associated with car park waterproofing. Finally we outline the full range of car park waterproofing services provide by Car Park Waterproofing Systems. Our aim is to help car park managers and owners make informed decisions about car park waterproofing.
Table Of Contents
- What Is Car Park Waterproofing?
- What Are The Benefits Of Car Park Waterproofing?
- What Are Car Park Waterproofing Systems?
- What Are The Different Types Of Car Park Waterproofing Systems?
- How Do You Waterproof A Car Park?
- How Much Does Car Park Waterproofing Cost?
- Our Car Park Waterproofing Services
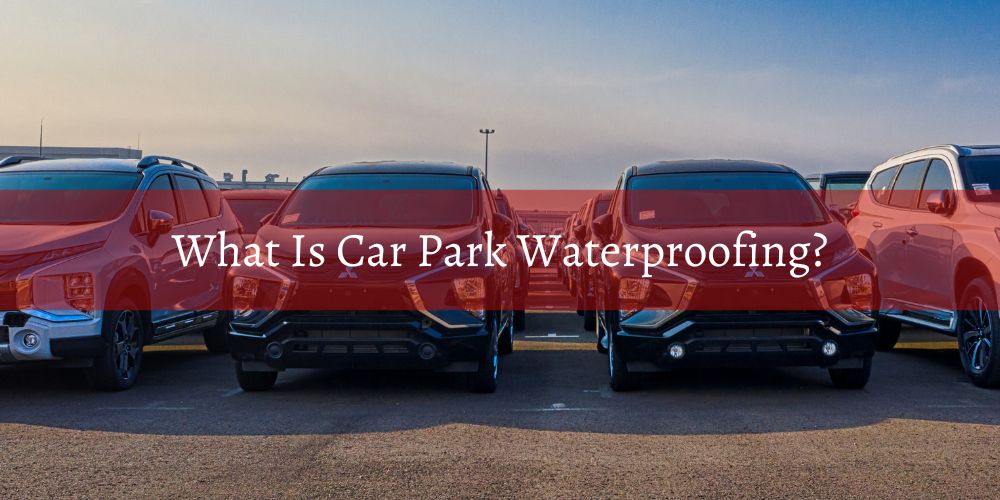
What Is Car Park Waterproofing?
Car park waterproofing is a process designed to protect parking structures from water ingress. Water ingress can cause significant deterioration to car park structures over time. Car park waterproofing involves the application of waterproof membranes or coatings to the surface of the parking structure. The waterproofing is applied to all surfaces in the car park including; ramps, intermediate decks, roofs and walkways. The primary aim of car park waterproofing is to prevent water infiltration which can lead to structural damage, corrosion of steel reinforcements, and concrete degradation. Effective car park waterproofing will maximise the lifespan of car parks whilst enhancing safety and maintaining the aesthetic appearance of the car park. The materials most often used for the waterproofing of car parks are mastic asphalt and liquid applied coatings. The car park waterproofing system chosen should have the following characteristics; the durability to endure vehicular traffic, high chemical resistance, UV stability and crack bridging properties. Below these characteristics are listed and explained in more depth.
- The Durability To Endure Vehicular Traffic
- High Chemical Resistance
- UV Stability
- Crack Bridging Properties
1. The Durability To Endure Vehicular Traffic
The durability to endure vehicular traffic refers to a surface or material's ability to withstand the wear, weight, and impact of continuous vehicle movement without compromising its structural integrity or performance. In car park waterproofing, the durability to endure vehicular traffic is crucial to ensure the waterproofing layer remains intact under heavy loads. This durability helps prevent water ingress and protects the underlying structure from long-term damage.
2. High Chemical Resistance
High chemical resistance refers to a material's ability to resist exposure to corrosive substances without degrading or losing its functional properties. These corrosive substances include; oils, fuels, and de-icing salts. Car parks are often exposed to these corrosive substances which means it is critical car park waterproofing have high chemical resistance. Car park waterproofing with high chemical resistance will protect the parking structure from vehicle fluids such as oils, fuels and deicing salt as well as chemicals used for maintenance and cleaning.
3. UV Stability
UV stability refers to a material's ability to resist degradation, discolouration, or reduced performance when exposed to prolonged ultraviolet (UV) radiation from sunlight. In car park waterproofing, UV stability is important for maintaining the integrity and effectiveness of exposed surfaces. UV stability is especially important for exposed car park decks such as top decks. Car park waterproofing with UV stability provides long-lasting protection against weathering and environmental damage.
4. Crack Bridging Properties
Crack bridging properties refer to a material's ability to flexibly span and seal cracks or gaps in a surface. Car park waterproofing with crack bridging properties fill cracks in a substrate which protects the parking structure from water ingress. When applying car park waterproofing to an existing parking structure crack bridging properties are critical to prevent water ingress through any cracks caused by thermal expansion, contraction, or heavy vehicle loads. However, it is important to note crack bridging properties will not remedy cracks over 3mm. If a crack is more than 3mm it will need to be pre-repaired.
Have a question about an upcoming project?
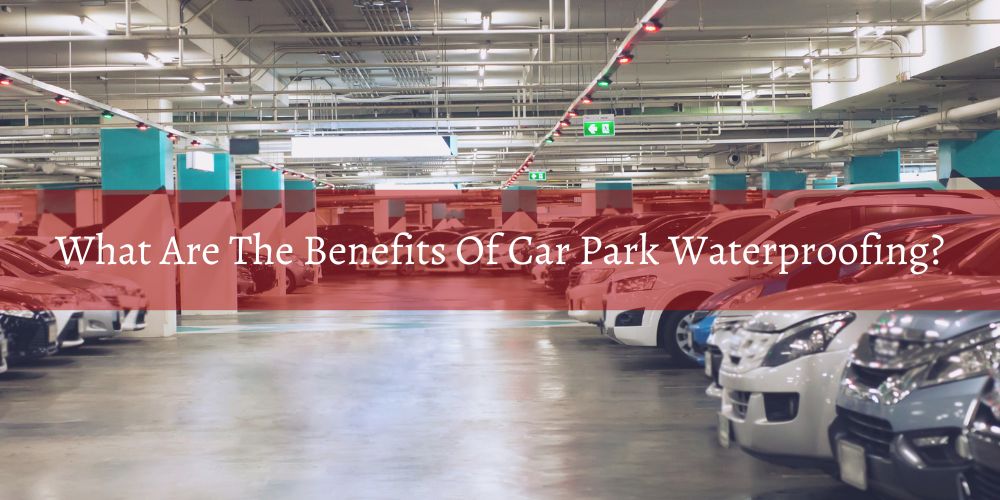
What Are The Benefits Of Car Park Waterproofing?
The benefits of car park waterproofing are; prolonged structural integrity, enhanced safety for car park users, increased car park lifespan, reduced car park maintenance costs, improved aesthetic appearance and the prevention of concrete degradation. The primary benefit of car park waterproofing is it prolongs the structural integrity of the car park structure by preventing water ingress. The list below explores each of the benefits of car park waterproofing in more detail.
- Prolonged Structural Integrity
- Enhanced Safety For Car Park Users
- Increased Car Park Lifespan
- Reduced Car Park Maintenance Costs
- Improved Aesthetic Appearance
- The Prevention Of Concrete Degradation
1. Prolonged Structural Integrity
Prolonged structural integrity is the major benefit of car park waterproofing. Structural integrity refers to the ability of a structure to withstand its intended load without experiencing failure, deformation, or collapse. Prolonging structural integrity means the safety and stability of a structure is extended. Car park waterproofing prolongs structural activity by preventing water from infiltrating and damaging the underlying structure. According to a study titled Review on Enhancing Building Resilience in Waterproofing Systems published in the International Journal of Research Publication and Reviews, “Waterproofing plays a crucial role in maintaining the structural integrity of buildings and various structures”. Car park waterproofing prevents water ingress which can cause significant damage to the structural components of a car park, particularly the steel reinforcements within concrete. When steel is exposed to water, it can rust and expand, increasing its volume by approximately 2 to 4 times. When concrete rusts and expands it can cause it to crack and spall. Concrete degradation can compromise the strength and stability of the entire structure, leading to costly repairs or even potential failures. This underlies the importance of effective car park waterproofing to protect the underlying structure.
2. Enhanced Safety For Car Park Users
Car park waterproofing should enhance the safety of car park users. Enhanced safety for car park users refers to measures and features designed to reduce risks and promote a secure environment for both pedestrians and vehicles. Car park user safety can be improved in the following ways; slip-resistant surfaces, clear markings, and adequate lighting. Car park waterproofing enhances safety by reducing slip hazards instigated by water pooling on surfaces. There is extensive research which highlights how flooring materials can prevent slip-related accidents. This research also states the importance of taking into account the environmental conditions of floor surfaces, in the paper Investigation of Floor Surface Finishes for Optimal Slip Resistance Performance published in Safety and Health at Work in 2017, it is concluded “floor surface finishes require different levels of surface coarseness for different types of environmental conditions to effectively manage slippery walking environments”. A good car park waterproofing system will be able to offer an anti-slip finish which can tolerate surface related slip risks like oil from cars and those induced by adverse weather conditions (snow and ice). When combined with adequate lighting the use of a car park waterproofing system with an anti-slip finish can greatly increase car park safety, this is amplified further in dark environments such as underground car parks or exposed car parks in the winter months.
3. Increased Car Park Lifespan
Car park waterproofing increases the lifespan of a car park. Car park lifespan refers to the length of time a parking facility remains functional, safe, and structurally sound. The lifespan of a car park is typically influenced by construction quality, maintenance practices, and environmental conditions. Car parks which are waterproofed benefit from significantly longer lifespans. The research paper Water proofing system in concrete structures by Sameer Khanna, Rohit Sah, Surendra Hooda and Deepak Kaushik from the International Journal of Research in Civil Engineering and Technology directly states “by preventing water from entering the concrete, waterproofing helps to extend the lifespan of the building and reduce maintenance costs in the long run”. Water ingress can lead to a car park having a variety of issues which can reduce its lifespan including; corrosion, and spalling. Waterproofing prevents corrosion and spalling by providing a barrier between the car park deck and the underlying structure. This barrier prevents corrosion developing which can lead to spalling.
4. Reduced Car Park Maintenance Costs
Car park waterproofing reduces maintenance costs. Car park maintenance costs refer to the expenses incurred in preserving the functionality, safety, and appearance of a parking facility through regular inspections, repairs, and cleaning. As mentioned in the research above, by preventing water from entering the concrete, waterproofing helps reduce maintenance costs in the long run. Water damage can cause a host of issues which will require repairs to be carried out. Typical car park repairs include; sealing cracks in parking decks, addressing corrosion and resurfacing degraded concrete. The British Parking Association's document Asset Management and Maintenance of Parking Structures states “water, combined with other pollutants energises degradation and whatever the form of construction (steel or concrete), the end result is the same”. This highlights the important role car park waterproofing plays in minimising the maintenance costs over a car park's service life. The document goes on to state “by the time the deterioration is visible through cracking, spalling or rust staining, the process is well underway and needs significant expenditure to control” which highlights how waterproofing can prevent significant car park maintenance costs. Car park waterproofing does not only financially benefit car park owners and operators by minimising maintenance costs, it also helps keep parking facilities operational.
5. Improved Aesthetic Appearance
Car park waterproofing improves the aesthetic appeal of a car park and the surrounding area by preventing water ingress. The aesthetic appearance of a car park refers to its visual appeal, this consists of surfaces, markings, design elements, and the state of the surrounding environment. A well maintained car park waterproofing system will improve aesthetic appeal by presenting an attractive seamless surface with clear markings. Waterproofing the concrete structures of car parks prevents efflorescence by preventing water infiltration. Efflorescence is the migration of water-soluble salts to the surface of a porous material, these water-soluble salts form a white or greyish powdery coating as the water evaporates. Efflorescence is commonly seen on construction materials like concrete, brick, and stone. The Concrete Network article Concrete Efflorescence - Causes, Removal & Prevention states “primary efflorescence is caused by the water in the concrete evaporating from the slab leaving behind the soluble salts on the concrete surface”. Car park waterproofing also prevents water stains, mould, mildew which can all make a car park look neglected and unattractive. A car park maintaining an attractive aesthetic appearance will improving user experience. A positive experience for car parks users is important for commercial properties such as shopping centres where appearance directly impacts customer satisfaction.
6. The Prevention Of Concrete Degradation
Car park waterproofing prevents concrete degradation. Concrete degradation is the process by which concrete deteriorates due to environmental factors, chemical reactions, and physical stresses, leading to a reduction in its strength, durability, and overall structural integrity. Concrete degradation is a frequent problem in car parks exposed to water. By providing a waterproof barrier car park waterproofing stops water ingress which causes concrete degradation. This is highlighted by Kari L. Yuers in a presentation for the American Concrete Institute titled Admixtures Part 2 Permeability Reducing Admixtures and Admixtures for controlling ASR which states “the most common mechanisms that deteriorate concrete all involve water”. When water penetrates concrete, it can cause deterioration. The deterioration is caused through processes such as freeze-thaw cycles, alkali-silica reaction, and sulphate attack. Freeze-thaw cycles can reduce concrete strength, which can lead to cracking, spalling, and weakening of the concrete structure. Applying a waterproofing membrane to the concrete deck of a car park creates a protective barrier which prevents water from reaching the concrete. Car park waterproofing preserves the strength and durability of the concrete. There are now eco-friendly car park waterproofing systems available which can protect against concrete degradation. The viability of eco-friendly car park waterproofing options is highlighted in the research paper Behaviour of concrete specimens retrofitted with bio-based polyurethane coatings under dynamic loads by H.M.C.C. Somarathna. This paper states “bio-based PU is a green material and application of PU coating provides a viable and sustainable technique for protecting concrete structures”. Effective car park waterproofing will prevent concrete decks from degrading, prolong structural integrity and maximise the lifespan of the car parks.
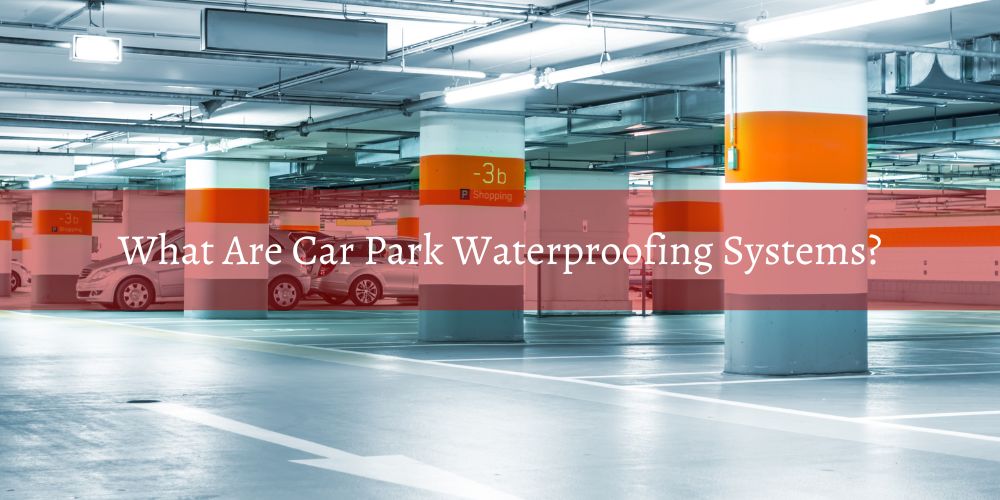
What Are Car Park Waterproofing Systems?
Car park waterproofing systems are specialist materials which prevent water infiltration into parking structures. Car park waterproofing systems consist of; a waterproofing membrane or coating, sealants, drainage solutions, anti-slip surfacing and line markings for parking bays. Mastic asphalt and liquid applied membranes are normally used for the waterproofing layer. The main objective of car park waterproofing systems is to protect the concrete and steel components of a car parks structure from water damage, corrosion, and deterioration.
What Are The Different Types Of Car Park Waterproofing Systems?
The different types of car park waterproofing systems are liquid-applied, mastic asphalt and cementitious. There are some other systems used but these three car park waterproofing systems are used for the majority of car parks in the UK. These three car park waterproofing systems are favoured for their durability and proven performance of preventing water infiltration. The list below looks at each of these car park waterproofing systems in more detail.
- Liquid-Applied
- Mastic Asphalt
- Cementitious
1. Liquid-Applied
Liquid applied waterproofing refers to the process of applying a liquid coating which cures to form a durable, seamless and watertight barrier which protects the substrate it encapsulates. Liquid applied coatings are ideal for car park waterproofing as they can easily be applied to complex layouts, this includes ramps and expansion joints. The ability of liquid membranes to cope with complex details ensures comprehensive protection against water ingress no matter the car park layout. Liquid coatings can also be finished with hard wearing top coats which can provide long-term durability despite the heavy traffic loads which modern car parks must endure. The leading liquid coatings for car parks are UV stable which make them a perfect choice for deck systems. Additionally, most liquid coatings are cold applied, which reduces disruption and safety concerns during installation as no hot works are required. The majority of liquid applied coatings used for car park waterproofing are polyurethane, polyurea or Polymethyl Methacrylate (PMMA). The leading car park waterproofing systems in the UK are Triflex Systems and Thrakon Desmoflex PU.
2. Mastic Asphalt
Mastic asphalt waterproofing is a highly durable, seamless, and flexible waterproofing solution made from a mixture of bitumen and aggregates, applied as a hot liquid which cools to form a tough, watertight layer. For car park waterproofing, mastic asphalt is ideal it can cope with heavy-traffic areas due to its ability to withstand significant loads, resist water ingress, and adapt to structural movement. Mastic asphalt can also be finished with a hard wearing top coat with anti slip properties. Car parks decks waterproofed with mastic asphalt will benefit from long term waterproofing protection. Legendary asphalt spreader John Taylor explained at a training course for RJ Evans the key to maximising the lifespan of a mastic asphalt car park is “all about maintenance, cars damage upstands, outlets get blocked” he also went on to add “if expansion joints are not prepared properly that's where a lot of asphalt cracks, expansion joints needs to be set so asphalt has the correct thickness to cope with traffic”. Despite the high cost of mastic asphalt, when installed and maintained correctly it is hard to find another waterproofing method which offers as good value for money.
3. Cementitious
Cementitious waterproofing is a durable, rigid waterproofing method which uses a combination of cement, sand and specialised chemicals to create a protective barrier against water ingress on concrete and masonry surfaces. In car park waterproofing, it is particularly effective for sealing foundations, retaining walls, and areas with minimal structural movement. Cementitious is a popular method of protecting parking decks against moisture and environmental damage. Cementitious waterproofing is easy to apply and has excellent compatibility with concrete substrates. The only instance where cementitious waterproofing may not be the ideal choice of waterproofing is on top decks with heavy vehicular usage, for such scenarios mastic asphalt and liquid coatings would normally perform better. However, cementitious waterproofing is an excellent solution for interior decks. The research paper Effect of Cementitious Capillary Crystalline Waterproofing Materials on the Mechanical and Impermeability Properties of Engineered Cementitious Composites published in PMC in 2023 states “total porosity of the structure decreased with increasing CCCW content”. This demonstrates cementitious waterproofing can effectively reduce the porosity of concrete structures, which enhances their resistance to water penetration.
Liquid applied, mastic asphalt and cementitious waterproofing all excellent options for car park waterproofing. These 3 waterproofing systems have demonstrated they have the ability to meet the demands of modern car parks. The choice of which car park waterproofing system to use will come down to the specifics of the project, namely budget, layout and usage. To ensure you choose the right solution it is always recommended to consult with a car park waterproofing contractor.
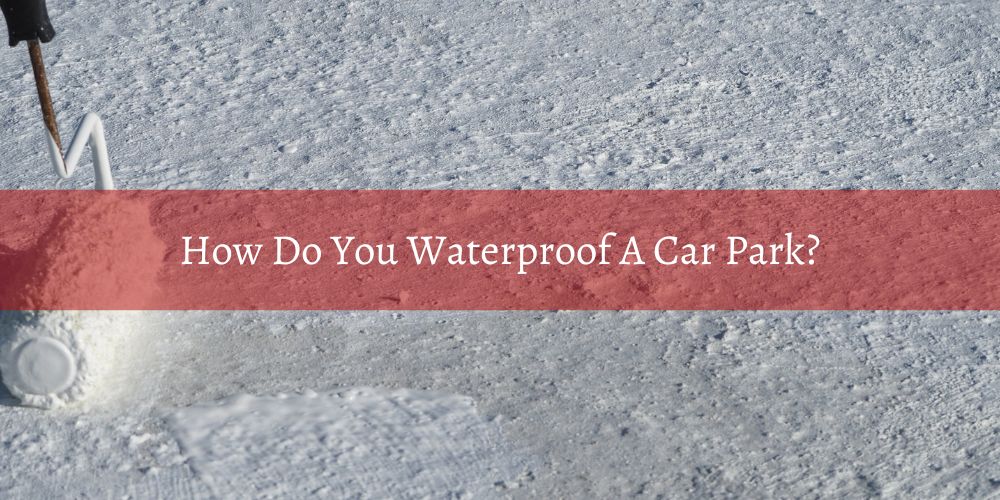
How Do You Waterproof A Car Park?
You waterproof a car park in the following 5 steps, car park surface preparation, priming the prepared car park surface, apply the waterproof layer to the car park deck, add a top coat to provide extra durability or anti-slip properties if required, then conduct a quality control inspection and set up a maintenance plan. The list below details the 5 steps involved in waterproofing a car park. It explains the process for both mastic asphalt and liquid applied waterproofing systems.
- Car park surface preparation.
- Priming the prepared car park surface.
- Apply the waterproof layer to the car park deck.
- Add a top coat to provide extra durability, slip or skid resistance (if required).
- Conduct a quality control inspection and set up a maintenance plan
1. Car Park Surface Preparation
Car park surface preparation is the process of cleaning the surface to remove dirt, debris, and contaminants. Then repairing any cracks, damaged or uneven areas to create a smooth, stable foundation for subsequent layers. The first step in car park surface preparation is cleaning. The car park surface can be cleaned in these ways; water jetting, air blowing or brushing. It is very important to ensure the surface is dry and free from any materials such as oil and grease which could impair adhesion of the waterproofing layer.
The second step in car park surface preparation is repairing any cracks, damaged or uneven areas in the surface. Cracks in the surface which are over 3mm are filled with a pu sealant, cracks under 3mm can be filled by the waterproofing layer if it has crack bridging properties. Surface irregularities must be addressed through planing. Planing is the process of removing layers or uneven sections of a surface to create a smoother, more even finish. Planing is often done using specialised machinery, such as a planer or milling machine to create a smooth base which will support an even application of the waterproofing layer. Cracks in the surface which are over 3mm are filled with a pu sealant, cracks under 3mm can be filled by the waterproofing layer if it has crack bridging properties. Surface damage such as spalling and pothole repairs is fixed by removing damaged or loose concrete. Then filling the holes in the surface with repair mortars or concrete patching compounds. Finally, it should be ensured the substrate has a good key base for adhesion to the waterproofing layer.
2. Priming the prepared car park surface.
Priming the prepared car park surface involves applying a specialised bonding agent to promote adhesion between the substrate and the subsequent waterproofing layer. The type of primer used will depend upon the chosen waterproofing layer, mastic asphalt will use a bitumen-based primer whereas the primer for liquid waterproofing will depend upon the system. It is important to ensure the primer is applied evenly across the car park surface to ensure complete coverage. The manufacturer’s instructions should be followed regarding the application rate and drying time.
The primer should seal the surface and promote adhesion between the substrate and the waterproofing layer, this can be tested with a peel test. A peel test is a quality control method used to measure the adhesion strength between layers, such as a primer and substrate or a primer and coating. The objective of a peel test is to ensure the proper bonding between layers. If a peel test fails the following steps should be followed; re-evaluate the surface preparation, ensure the primer was applied correctly and analyse the substrate compatibility with the primer. Then a decision should be made to either reapply the primer or to use a more suitable primer.
3. Apply the waterproof layer to the car park deck.
Applying the waterproofing layer to the car park deck involves applying a protective membrane or coating over the prepared and primed surface to create a seamless, durable barrier against water ingress and environmental damage. Most liquid applied waterproofing systems will be applied by brush, roller or spray. Liquid systems may need multiple coats, with extra coats often enhancing the durability and effectiveness. Each layer should be left to cure in accordance with the manufacturers guidelines. Curing time may vary depending on ambient temperature and humidity. A specialist detailing product or reinforcement membrane may be required for complex details such as drains, edges and upstands.
Before mastic asphalt is applied to the primed car park surface a separating membrane must be laid. This separating membrane is a 10mm roofing underlay on fibreglass tissue. There are 4 reasons this separating membrane is laid; it prevents adhesion, serves as a moisture barrier, protects the substrate from high temperatures and allows for movement. Once this separating membrane is laid it is time to apply the mastic asphalt waterproofing. Mastic asphalt will nearly always be applied with a wooden float. The waterproofing layer of mastic asphalt is applied with one or two coats of roofing grade mastic asphalt. These coats should be spread evenly to ensure a uniform layer across the car park surface.
4. Add a top coat to provide extra durability or anti-slip properties (if required)
Adding a top coat involves applying a final protective layer over the waterproofing system to enhance durability, improve resistance to wear, or provide anti-slip properties for increased safety and longevity. For liquid applied systems a top coat with excellent wear and impact resistance is applied over the waterproofing layer, these are often available in coloured finishes to match the colour scheme of the project. Top coats are normally applied in two layers. Top coats are often capable of having anti-skid properties, this is achieved by adding 0.1 to 0.3 millimetres of quartz to the product before application. Anti-skid properties can also be enabled by spreading 0.1 to 0.5 millimetres of quartz or silica sand on the first of the two of the top coat. Once the top coat has dried excess quartz or silica sand should be brushed away. Top coats should normally be applied within 3 to 4 hours of the waterproofing layer being applied.
For mastic asphalt, extra durability is achieved by adding a one coat of paving grade mastic asphalt. This layer normally consists of 30% grit to provide added hardness. In some cases, 40% grit can be used if the area must endure high demands. An example of a car park deck which must endure high demands would be loading bays with pallet trucks. Leading asphalt spreader John Taylor mentions “using 40% grit can make it challenging to achieve a proper seal”, this means it should be carefully considered whether the car parks demands definitively require 40% grit paving grade asphalt. When apply a wear coat of paving grade asphalt it must be applied smoothly and compactly. If the car park deck requires skid resistance, a crimp roller can be used to provide the necessary friction. The use of a crimp roller reduces the need for an additional anti-slip coating.
5. Conduct a quality control inspection and set up a maintenance plan
Conducting a quality control inspection involves thoroughly examining the completed work to ensure it meets specified standards, including adhesion, uniformity, and overall performance, before final approval. For liquid waterproofing once the membrane has cured, the entire surface should be inspected for imperfection or areas with insufficient coverage. If any defective areas are identified they should be repaired or rectified. An example would be applying more liquid coating to an area which did not receive adequate coverage.
In the case of mastic asphalt, once it has cooled and set the surface should also be inspected for imperfections or weak stops. The thickness of the mastic asphalt membrane should be consistent throughout and the surface should be completely sealed. Any parts of the surface including the detailing which do not meet the required standards should be repaired immediately. The final step for car parks waterproofed with both liquid coatings or mastic asphalt is to put a maintenance plan in place.
A maintenance plan is a structured schedule of regular inspections, repairs, and upkeep designed to ensure the continued functionality, safety, and longevity of a system or structure. For car parks waterproofed with mastic asphalt or liquid coatings, a maintenance plan helps maximise the lifespan of the car park. By identifying and address minor issues early, the risk of water ingress and surface deterioration is minimised which can lead to significant savings to the car park owner over the car parks service life.
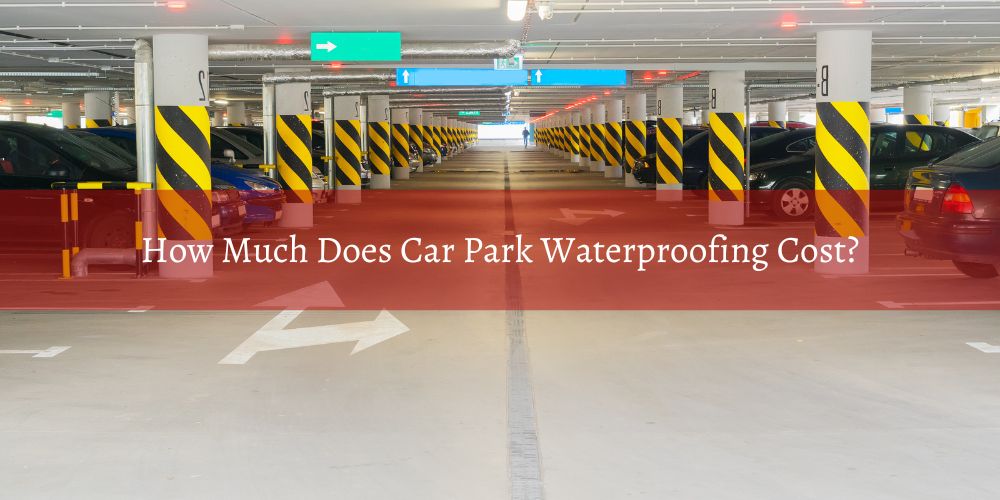
How Much Does Car Park Waterproofing Cost?
The cost of car park waterproofing is between £40.00 and £180.00 per square metre in most cases. However, this varies depending on the type of system used. The table below provides an overview of the estimated costs for the three most common waterproofing systems, expressed in pounds per square meter (£ per SQM). These estimates can help you plan your budget based on the specific needs and requirements of your car park project.
Car Park Waterproofing System | Cost per Square Metre (£ GBP) |
---|---|
Liquid Applied Membranes | £48 to £60 |
Mastic Asphalt | £160 to £180 |
Cementitious Waterproofing | £40 to £55 |
*These estimates are general and actual costs can vary based on specific project requirements, location, and market conditions.